Extrusion blow molding principle
In the extrusion blow molding process, a semi-molten tube blank (parison) obtained by extrusion or injection molding is placed in a mold of various shapes, and compressed air is introduced into the tube blank to inflate it so as to be in close contact with the mold. On the wall of the chamber, the mold is cooled and released to obtain a extrusion product. The forming process includes the manufacture of plastic parisons and the blow molding of parisons. This molding method can produce various packaging containers such as bottles, pots and barrels with different calibers and different capacities, daily necessities and children’s toys.
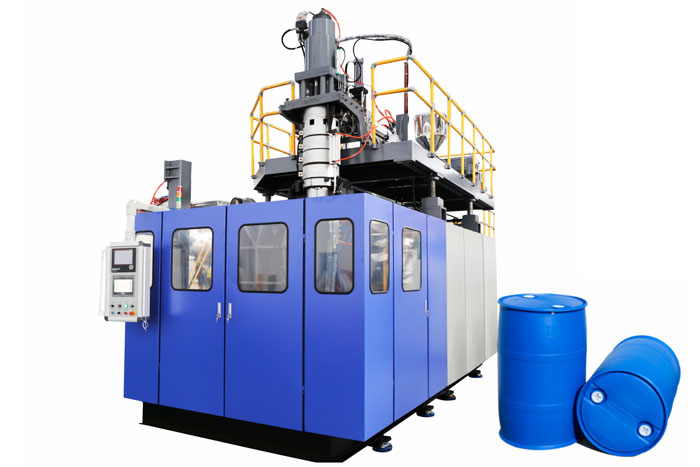
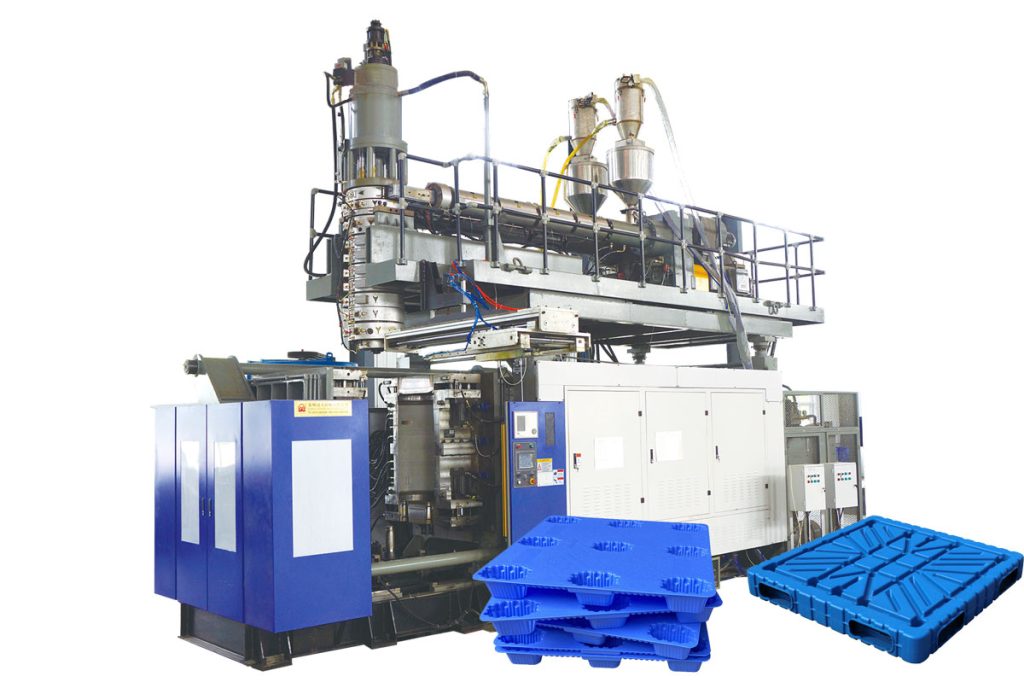
Plastics used for extrusion blow molding include polyethylene, polyvinyl chloride, polypropylene, polystyrene, linear polyester, polycarbonate, polyamide, cellulose acetate, and polyacetal resins. Among them, the consumption of high-density polyethylene is the first. It is widely used in the packaging of food, chemical and process liquids. High molecular weight polyethylene is suitable for the manufacture of large fuel tanks and barrels. Polyvinyl chloride is widely used in the packaging of cosmetics and detergents because of its good transparency and air tightness. With the development of non-toxic polyvinyl chloride resins and auxiliaries, as well as the development of stretch blow molding technology, the use of polyvinyl chloride containers in food packaging has increased rapidly and has begun to be used in beer and other beverages containing carbon dioxide gas beverages. . Linear polyester materials are new materials that have entered the field of extrusion blow molding in recent years. Due to its glossy appearance, excellent transparency, high mechanical strength and good preservation of the contents of the container, the waste incineration treatment does not pollute the environment, so the development of the bottle is very fast, especially It is the most widely used in pressure-resistant plastic food containers. Due to the improvement of its resin modification and processing technology, the use of polypropylene has also increased year by year.
Extrusion blow molding can basically be divided into two categories: extrusion-blow molding and injection-blow molding. The main difference between the two is the preparation of the parison, and the subsequent blowing process is basically the same. Based on these two molding methods, extrusion-stretching-blow molding (referred to as extrusion-pull-blowing), injection-stretching-blow molding (referred to as injection-pulling) and multi-layer reflection Plastic and so on.
Plastics used for extrusion blow molding include polyethylene, polyvinyl chloride, polypropylene, polystyrene, linear polyester, polycarbonate, polyamide, cellulose acetate, and polyacetal resins. Among them, the consumption of high-density polyethylene is the first. It is widely used in the packaging of food, chemical and process liquids. High molecular weight polyethylene is suitable for the manufacture of large fuel tanks and barrels. Polyvinyl chloride is widely used in the packaging of cosmetics and detergents because of its good transparency and air tightness. With the development of non-toxic polyvinyl chloride resins and auxiliaries, as well as the development of stretch blow molding technology, the use of polyvinyl chloride containers in food packaging has increased rapidly and has begun to be used in beer and other beverages containing carbon dioxide gas beverages. . Linear polyester materials are new materials that have entered the field of extrusion blow molding in recent years. Due to its glossy appearance, excellent transparency, high mechanical strength and good preservation of the contents of the container, the waste incineration treatment does not pollute the environment, so the development of the bottle is very fast, especially It is the most widely used in pressure-resistant plastic food containers. Due to the improvement of its resin modification and processing technology, the use of polypropylene has also increased year by year.
Extrusion blow molding can basically be divided into two categories: extrusion-blow molding and injection-blow molding. The main difference between the two is the preparation of the parison, and the subsequent blowing process is basically the same. Based on these two molding methods, extrusion-stretching-blow molding (referred to as extrusion-pull-blowing), injection-stretching-blow molding (referred to as injection-pulling) and multi-layer reflection Plastic and so on.